"Excellence in Finishing, Engineered for You."
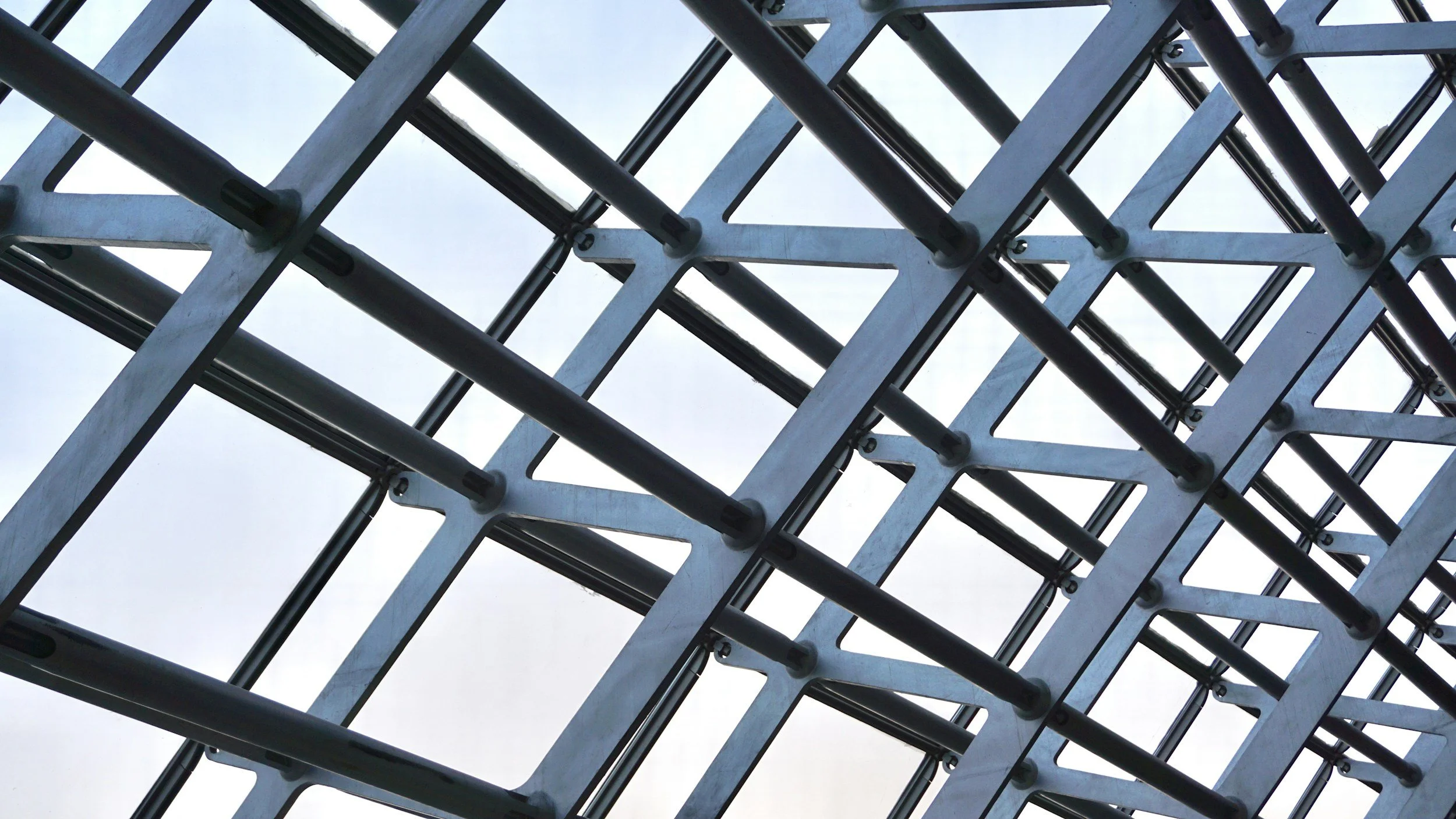
Here to serve and support you and your customer(s):
Tailored Finishing Processes
High standards (ISO Certified)
Quick Turnaround Job Shop
Consistent Communication & Results
Our Services
-
Abrasive Flow Machining
Abrasive Flow Machining is a highly specialized service that is particularly effective for parts that require a unique and precise internal surface finish. This is a great technique to use for Additive Manufacturing (AM) parts.
-
Air Blasting
Air blasting is a highly effective method for efficiently removing various contaminants or surfaces on parts using abrasive media that is propelled with air.
-
Wheel Blasting
Wheel blasting is an efficient process that utilizes high-velocity steel shot that is propelled by a rotating wheel, to clean, strengthen, or prepare metal surfaces for further finishing.
-
Vibratory Tumble Deburr & Polishing
Vibratory tumbling is a process that is essential for achieving precise surface finishes in mass quantities.
-
Precision Hand Deburring
The precision hand deburring process involves skilled technicians meticulously removing sharp edges and burrs from metal or plastic components to ensure a smooth and safe finish.
-
Sand Blasting
This abrasive blasting process offers exceptional surface preparation and finishing. We eliminate contaminants and imperfections for optimal coating adhesion or the next steps in the finishing process.
-
Outsource Partnerships & Services
We have meticulously built a strong network of reliable and trustworthy partners that offer a wide range of quality services that compliment what we do.
-
Value-Added Services
Value-added services at Engineered Finishing Inc. enhance our core offerings, providing customers with tailored solutions that improve efficiency, reduce costs, and ensure superior quality throughout.
Industries We Serve
At Engineered Finishing Inc., we firmly believe that collaborating with companies across a diverse range of industries is essential to fostering growth and innovation in the United States.